Next Woman Up: Ebony Short, Sewing Manager for the Baltimore Ravens
- Next Woman Up: Hannah Gordon
- Charlotte Jones
- Amina Edwards
- Kim Pegula
- Katie Blackburn
- Tina D'Orazio
- Tina Tuggle
- Gayle Benson
- Kim Rometo
- Ashley Lynn
- Karen Murphy
- Amy Sprangers
- Lara Juras
- Megan McLaughlin
- Nadege Pluviose
- Kalen Jackson
- Nancy Meier
- Kelly Kleine
- Mindy Black
- Hayley Elwood
- Sarah Hogan
- Chanelle Smith-Walker
- Gina Newell
- Molly Higgins
- Tiffany Morton
- Maria Rodriguez
- Chloe Janfaza
- Gabrielle Valdez Dow
- Kristi Johnson
- Kelsey Henderson
- Fouzia Madhouni
- Jackie Maldonado
- Stephanie Kolloff O’Neill
- Alexandra Cancio-Bello
- Ashton Washington
- Qiava Martinez
- Remi Famodu-Jackson
- Emily Starkey
- Ciara Burgi
- Robin DeLorenzo
- Marissa Figueroa
- Angela Baker
- Emily Griffin
- Phoebe Schecter
- Alexis Dotson
- Nancy Gold
- Ameena Soliman
- Tameka Rish
- Sarina Soriano
- Maria Gigante
- Ebony Short
- Shelly Harvey
- Sarah Mallepalle
- Maya Ana Callender
- Melainey Lowe
- Donny Brock
- Lacy Ekert
- Sarah Evans
- Darline Llamas Llopis
- Jaemin Cho
- Blayre Holmes Davis
- Michelle Xiao
Women are rising up the ranks throughout professional football, earning positions of power in a space that for too long was ruled almost exclusively by men. We’re seeing more and more women breaking barriers in the sport, but what are the stories beyond the headlines? Who are the women shaping and influencing the NFL today? Answering those questions is the aim of the Next Woman Up series. While the conversational Q&As are edited and condensed for clarity, this is a forum for impactful women to share experiences in their own words. Without further ado, we introduce:
Ebony Short, Baltimore Ravens
Position: Sewing Manager
Can you talk me through your career path and how you ended up with the Ravens?
I learned very quickly that my career path is very peculiar to others in the organization. Most people knew they wanted to work in sports. I went to Parsons School of Design in New York. My first job out of college was with Parson-Meares, a costume shop in New York. It’s a big company that does costumes for Broadway, such as The Lion King, Cinderella and Pippin, and other live performances. I was with them for a few years and learned a lot very quickly. In that job, I worked a lot on the hyenas for The Lion King. The Broadway costumes are so intricate, so that job let me flourish artistically. I love to paint and draw, too, so they gave me space to use that creativity. To this day, I am always trying to add some creativity to things. I also worked with a lot of different materials in that job and learned some engineering with those costumes.
One of the first shows I worked on was Cinderella, and one of the quick costume changes was for the fairy godmother. She was dressed in rags, and we had to figure out how to get individual pieces and connect it all together into this magical dress. I was hired to mostly be a dressmaker, but because I was so willing to help others and learn, I learned things I never would have. We built her wings that were made from medal rods and used the string from her cape that hid her hunchback — which was actually the costume change — to trigger the transformation. Working on projects like that opened my eyes to so much more. I learned to problem solve and think about how to elevate costumes.
I also worked other gigs on the side, like installing shows on cruise ships, while I was at Parsons. Then I went to John Kristiansen, another costume shop that did projects for shows and movies. I was in New York for probably 10 years, and I was constantly adding to my toolbox of skills, learning how to apply things from others into my own pieces.
In 2019, my plan was to go to California to fit Cher for costumes for her upcoming tour and work on some movies. But I’m originally from Maryland and was visiting my family there, and my sister told me she saw an opening for a sewing manager position at the Ravens. I remember thinking, What IS this job? My family loves football, and I grew up watching the Ravens, so it was a job that would make sense for me, if it was a fit. I went to the interview and was surprised to see what it all entailed. It was way more than I anticipated.
Wow, what a fun journey! Having been with the Ravens for several years now, can you describe what your role entails?
In our department, we have four seamstresses, and there is no way we would be able to do what we do without them and their skills. We make 3,700 thigh and knee pads in the offseason, along with specialty butt and hip pads, and sew them all into the players’ pants. We also sew all of the pockets and the name embroidery. Every time the Ravens sign a new player, we are sewing their name onto the jersey to make sure it is ready by the time the player arrives.
Another big part of our job is the custom alterations. We take care of the coaches a little bit for game day, but our main focus is the players. Our jerseys are a very specific fit, and you don’t want them to be too loose that you’re being tackled or too tight that the player can’t breathe. We’ve had to open seams in the shoulders so guys have more mobility, especially with our offensive linemen because their arms are always forward. Basically anything and everything a player needs, I will try to make that possible. Sometimes the equipment manager will explain what the player needs, but the players also come to us to show us a certain move that they can’t do because the jersey is too restricting. Then I know the exact alteration that needs to be made. It takes a lot of workshopping, but once we have it down, we can specialize all of that player’s jerseys. Same goes for the pants. We want to make sure every player is comfortable, so they don’t have to think about their uniform while they are playing.
Training camp is probably the busiest time of the year, but it’s helpful for us to see the players in their jerseys out at practice. I get most of my information then and in the first few weeks of the regular season. I think some players are surprised, in a sense, that we make jerseys fitted to them because maybe they haven’t had that before.
I also started painting cleats. Sometimes our players want a specific style of cleat, but maybe it only comes in bright orange. I will then paint them to be our colors, using a brush or an airbrush.
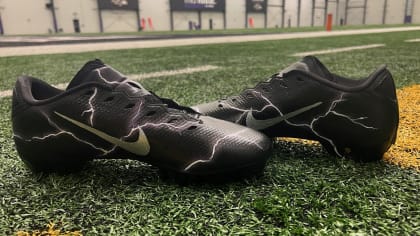
That’s interesting. So how many sets of uniforms do the players go through throughout the season? Are they replaced if there are stains from grass or poor weather?
I feel like I stopped counting because players trade a lot of jerseys now. But every player has a main and backup set for each game. Then they use two sets for practice. After a game, the team services department will wash the jerseys or send them to the cleaners to get them as clean as they can. If a jersey is completely ruined, we will get a new one, but they come back clean for the most part. Then the jerseys come to us and we check for the smallest of repairs because we want them looking great for game day. However, we will likely do new jerseys for prime-time games because all eyes are on us for those games. The turnaround is fast. The jerseys get cleaned Monday, so we basically get Tuesday to flip the jersey because we are packing for the next week’s game on Wednesday.
We also are in charge of sewing patches onto our practice and game jerseys. Our rookies have premier patches when they play their first games. When Calais Campbell was here, he won the Walter Payton Man of the Year, so every jersey he wore — even at practice — would have the Man of the Year patch. We also do sponsorship patches, and all of the practice jerseys have patches for accomplishments, including offseason workouts or playoffs.
What would you say is the most challenging part of your job?
It’s probably the quick turnaround during the week because sometimes uniforms come in late. It can take 30 minutes to repair a jersey, and that’s if you’re working fast. It can take a lot of time if there are a lot of jerseys to flip, alongside everything else we’re doing to get ready for the next game. It is tough to get everything set in a day.
We pack extras of everything for the games. Every player has two jerseys — a game set and a backup set. We’ll give each player a pair of pants, and we bring a bunch of other pants, some with pads or pockets. If a player has a special alteration, they will have their own pair. For example, some players have tights sewn into their pants, so they will have extra of that.
Let’s turn to mentorship. Do you have any mentors who have helped you in your career?
I guess not in the traditional sense, but I have learned so much from everyone who has been willing to share their skills with me throughout the years. John Kristiansen is one. He owned the shop, but was close with his employees. He knew I was into fashion, so he would explore ways to help me get projects to flourish in that space. I had so many co-workers who taught me new skills, as well. I really honed my skills because you never know when you might need them down the road. I’ve worked with so many different materials, and because I’ve always been willing to try new things, I have added a lot to my toolbox.
The people I’ve been around were always working to perfect their craft and I’ve learned something from everyone. They would always say, “Be great at what you do, and be meticulous.” I have really taken that to heart. That’s what I’ve tried to do, and I think it has paid off in boatloads.
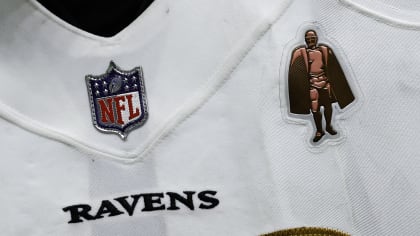
Do you have any advice for women interested in a career similar to yours?
My immediate thought is to be undeniable. I struggled a little bit at first when I took a job in sports because I had never been in a space like this. But I had to realize I belonged here and to let my work speak for me. That’s always my goal, to work really hard and leave people with a good impression of my work.
So that, and show up full. I think society in general teaches women to shrink themselves, especially in the workplace and in male-dominated industries. It’s easy to fall into the shadows. I am an introvert, but I’ve learned to speak up and do the work, so my full self shows up every day. What you have to say, do and offer is valuable. I’ve been so fortunate because I’ve had leadership that has seen that in me and allowed me to grow. Show up full because you are valuable, otherwise you wouldn’t have been hired.
That’s great advice. And lastly, what are you most proud of?
When I was 18 years old and decided to study design, there were people who thought I wouldn’t be able to sew for a career. A lot of people think there is one track for a career like this, but I’ve had a wide-ranging career, traveling the world and working on amazing projects. I’m proud of that and the fact that I’ve shown others that there is a whole world out there for sewing.
My first year with the Ravens was 2019, and we had an amazing season. That whole year was very exciting. We were winning, but I was also building this department. At the time, we had a few women who were sewing pads into pants, and they were doing minimal alterations. I’ve been very fortunate to have leadership who have supported me and my vision.
So I’m most proud of how much we’ve grown as a department, and I feel like we’re still just getting started. We have expanded our alterations and what we offer to the players for their uniforms. I am happy to have a department that the players feel comfortable coming to and where they feel seen.